The Vital Role of Mill Rolls in Metal Processing.
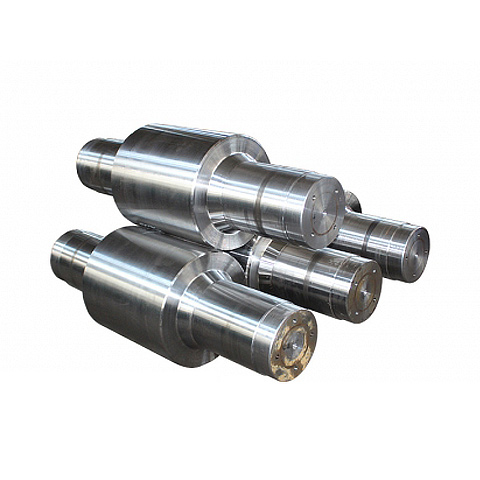
Mill rolls, also known as rolling mill rolls, are specialized parts of the mill that plays a key role in the metal processing field, from steel to aluminum, copper and other industries. They are used in rolling mills to reshape and reduce the thickness of metals, while also enhancing the mechanical properties of materials. From hot rolling, wire rods, section steel to cold rolling, the rolls endure extreme pressures and temperatures to deliver the desired products.
Technology of mill rolls--
A rolling process involves passing a metal billet through a pair of mill rolls. The roller central core is of tough materials, and the outer layer designed with a certain hardness and wear resistance. The rolls exert immense pressure, causing the material to deform and take on a new shape. The precise contours of the rolls determine the final dimensions and surface quality of the material.
Types of mill rolls--
Work rolls: These rolls come in direct contact with the rolled materials. Work rolls endure the most significant stress during rolling operations. They possess exceptional hardness, toughness, and resistance to thermal shock to withstand the intense conditions.
Backup rolls: Backup rolls provide support and prevent deformation of the work rolls. They are larger and stronger, often made from different materials to better absorb the forces transmitted through the work rolls.
Intermediate rolls: Positioned between the work and backup rolls, intermediate rolls help control the shape and thickness of the rolled materials as it passes through the mill. They contribute to achieving uniformity in the final product.
Materials of mill rolls--
The commonly used materials are cast iron rolls, cast steel rolls, forged steel rolls and combined rolls.
The evolution of mill roll technology continues to push the boundaries of what is achievable in metal processing. High-strength alloys, composite materials and advanced coatings have extended the lifespan of rolls while improving their efficiency; CNC technology and precise machining have allowed manufacturers making rolls with complex profiles that optimize the rolling process. It promotes the transformation of raw materials into dynamic industrial products.
Technology of mill rolls--
A rolling process involves passing a metal billet through a pair of mill rolls. The roller central core is of tough materials, and the outer layer designed with a certain hardness and wear resistance. The rolls exert immense pressure, causing the material to deform and take on a new shape. The precise contours of the rolls determine the final dimensions and surface quality of the material.
Types of mill rolls--
Work rolls: These rolls come in direct contact with the rolled materials. Work rolls endure the most significant stress during rolling operations. They possess exceptional hardness, toughness, and resistance to thermal shock to withstand the intense conditions.
Backup rolls: Backup rolls provide support and prevent deformation of the work rolls. They are larger and stronger, often made from different materials to better absorb the forces transmitted through the work rolls.
Intermediate rolls: Positioned between the work and backup rolls, intermediate rolls help control the shape and thickness of the rolled materials as it passes through the mill. They contribute to achieving uniformity in the final product.
Materials of mill rolls--
The commonly used materials are cast iron rolls, cast steel rolls, forged steel rolls and combined rolls.
The evolution of mill roll technology continues to push the boundaries of what is achievable in metal processing. High-strength alloys, composite materials and advanced coatings have extended the lifespan of rolls while improving their efficiency; CNC technology and precise machining have allowed manufacturers making rolls with complex profiles that optimize the rolling process. It promotes the transformation of raw materials into dynamic industrial products.